
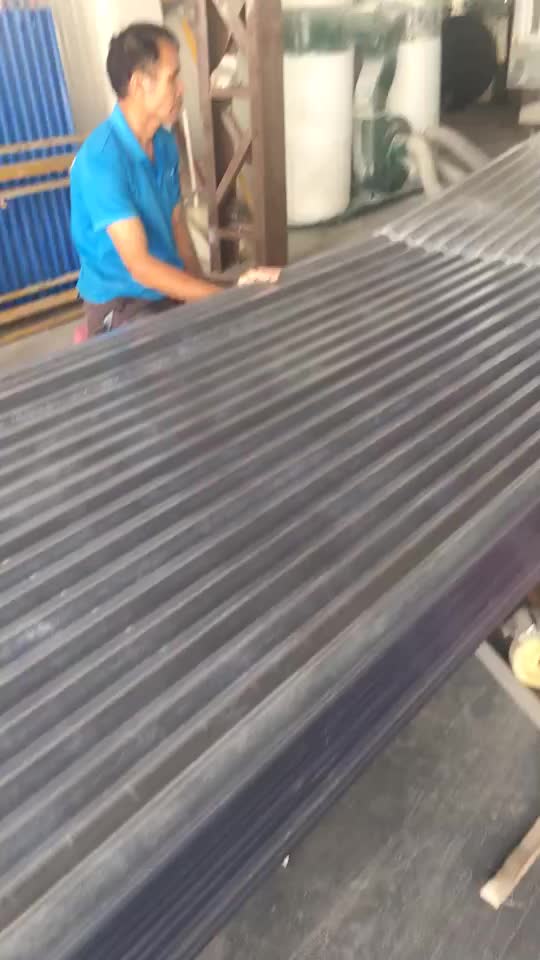
So a 1.5” wide (.13 ft) stud that is 9ft tall would give you a single component R value of 3.5 for more than an entire square foot (0.13ft x 9ft = 1.13sqft) of wall service area. Wood has an average R value of around 1 per inch – so a 2×4 stud (actually 1.5” x 3.5”) has an R value of 3.5. Fiberglass batt insulation is rarely installed properly and even when it is you most often have a 2×4 stud every 16 inches. However almost no one builds homes under laboratory conditions. laboratory) conditions the stated R values on products should hold true. These tests were developed with the strong influence of the fiberglass industry and as long as you are looking at a 100% covered section of a material under IDEAL (i.e. The term “R value”, (for Resistance value) was termed to quantify the thermal resistance of a material – or its ability to NOT conduct thermal energy (whether hot or cold). Over 50 years ago the fiberglass industry started working with the government to standardize the measuring of a product’s insulative properties.
#FIBERGLASS SIP PANELS ZIP#
The outer surfaces (also called “skins”) can be oriented strand board (OSB), Huber ZIP panels, LP Smartside panels or plywood, with various other sidings for non-structural applications. A 6-1/2″ (16.51 centimeters) thick panel has a nominal R-value of 40 (compared to the effective R-15 for fiberglass or open cell spray foam insulation in a typical 2×6 stud wall) (all the stated R-values are at 52º F the R-value of an Eco-Panel improves as the temperature drops). A typical Eco-Panels 4-1/2 inch (11.43 centimeters) thick panel has a nominal R-value of 26 (compared to the effective R9-10 for fiberglass or open cell spray foam insulation in a 2×4 stud wall). There are no clumsy splines to insert as with most other SIP products. Multiple panels can be quickly and easily joined together via an embedded cam-locking and tongue-and-groove rail system ensuring a sealed, tight fit.

Windows, doors, beam pockets and electrical conduit can be framed in our factory prior to injecting the foam ensuring the tightest possible seal against air and moisture penetration and avoiding this kind of modification on the jobsite. Our panels are manufactured by injecting polyurethane foam between two siding materials in a tightly enclosed cavity. Our panels are designed to carry the entire range of structural loads in a building and we can normally provide up to a 4x safety margin where normal building systems typically only achieve a 3x margin. While most commonly used for exterior walls, our panels can also serve as a load-bearing floor and ceiling/roof. Eco-Panels can provide your structure with the best thermal/structural envelope on the market today.

These panels, when connected together, take the place of a traditional 2×4 or 2×6 wall and insulation, providing superior structural support and insulation (resistance to the transfer of heat, cold, sound, vibration, etc). Eco-Panels manufactures a superior type of structural insulated panel (SIP), otherwise known as a sandwich panel or stressed-skin panel.
